精益生产:制造业职业安全与健康的革新之道
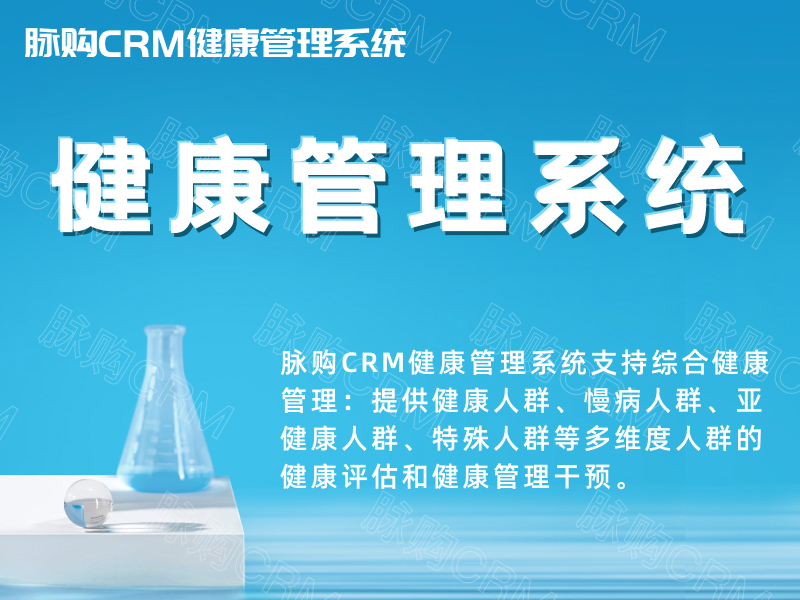
在制造业中,职业安全与健康始终是企业关注的核心议题。然而,传统的安全管理方式往往过于依赖规章制度和事后补救,忽视了预防和效率的提升。精益生产理念,以其独特的视角和方法,为制造业的职业安全与健康带来了全新的解决方案。本文将深入探讨精益生产如何在制造业中实现安全与健康的优化,为企业创造更大的价值。
一、精益生产的本质:消除浪费,提升效率
精益生产源于丰田生产系统,其核心理念是通过消除八大浪费(过量生产、等待、运输、过度加工、库存、动作、制造不良品和未利用的人才)来提高(
脉购CRM)生产效率。这一理念同样适用于职业安全与健康领域。通过识别并消除可能导致事故或职业病的风险因素,我们可以预防潜在的伤害,同时提高生产效率。
二、预防优于治疗:精益生产与风险管理
在精益生产中,预防被视为优于治疗。这意味着在事故发生前就应识别并消除风险。例如,通过定期的安全审计和风险评估,企业可以发现潜在的危险源,然后采取措施进行改进。这种前瞻性的风险管理策略,不仅降低了事故发生的可能性,也减少了因事故导致的停机时间和损失。
三、持续改善:5S与安全文化
精益生产中的5S(整理、整顿、清扫、清洁、素养)是提升工作环境和操作流程的重要工具。在职业安全与健康方面,5S可以帮助创建一个整洁、有序的工作环境,减少因混乱和杂(
脉购健康管理系统)乱导致的事故。同时,5S的实施也能培养员工的安全意识,形成积极的安全文化。
四、员工参与:激发内在动力,提升安全意识
精益生产强调全员参与,这在职业安全与健康中同样重要。通过鼓励员工参与安全改进活动,如提出改进建议、参与安全培训,可以增强他们的责任感和归属(
脉购)感,从而提高他们的安全行为。员工的积极参与不仅能发现更多的安全隐患,也能提升整体的安全水平。
五、精益生产与事故响应:快速恢复,减少损失
即使在事故发生后,精益生产也能提供指导。通过建立快速响应机制,企业可以在事故发生后迅速恢复正常生产,减少损失。同时,每一次事故都是学习和改进的机会,精益生产强调从事故中汲取教训,防止类似事件再次发生。
总结,精益生产理念为制造业的职业安全与健康提供了全面而有效的管理框架。它强调预防、持续改善、员工参与和快速响应,旨在消除浪费,提升效率,同时也保障了员工的健康与安全。在日益竞争激烈的市场环境中,采用精益生产理念,无疑能帮助企业实现可持续发展,赢得竞争优势。
文章信息仅供参考,不作为医疗诊断依据。
文章内容如有引用其他品牌或商标,如有侵权,请发邮件:724792780@qq.com,我们确认无误后会立即删除相关品牌或商标的引用情况。